Porosity in Welding: Identifying Common Issues and Implementing Ideal Practices for Prevention
Porosity in welding is a pervasive issue that commonly goes undetected up until it triggers considerable issues with the stability of welds. In this conversation, we will certainly explore the crucial variables adding to porosity development, analyze its destructive results on weld efficiency, and go over the best methods that can be embraced to decrease porosity incident in welding procedures.
Typical Sources Of Porosity

Utilizing filthy or damp filler products can present pollutants right into the weld, contributing to porosity issues. To mitigate these common causes of porosity, extensive cleaning of base metals, proper securing gas option, and adherence to optimum welding parameters are important methods in achieving top notch, porosity-free welds.
Impact of Porosity on Weld Quality

The presence of porosity in welding can substantially compromise the structural honesty and mechanical properties of welded joints. Porosity produces gaps within the weld steel, damaging its overall stamina and load-bearing capability.
One of the key effects of porosity is a reduction in the weld's ductility and durability. Welds with high porosity degrees often tend to display reduced effect strength and lowered capability to deform plastically prior to fracturing. This can be specifically worrying in applications where the welded elements undergo dynamic or cyclic loading problems. Porosity can impede the weld's capacity to effectively send forces, leading to premature weld failure and possible security hazards in essential structures. What is Porosity.
Ideal Practices for Porosity Prevention
To improve the structural honesty and quality of bonded joints, what particular procedures can be executed to reduce the incident of porosity during the welding procedure? Making use of the appropriate welding method for the details material being welded, such as adjusting the welding angle and weapon setting, can further protect against porosity. Regular evaluation of welds and prompt remediation of any kind of issues identified during the welding see here now process are crucial methods to stop porosity and generate high-quality welds.
Importance of Appropriate Welding Strategies
Applying appropriate welding methods is critical in ensuring the structural integrity and high quality of welded joints, building upon the foundation of reliable porosity prevention steps. Extreme heat can lead to boosted porosity due to the entrapment of gases in the weld pool. Additionally, utilizing the ideal welding parameters, such as voltage, current, and travel speed, is essential for accomplishing sound welds with very little porosity.
In addition, the selection of welding procedure, whether it be MIG, TIG, or stick welding, must straighten with the details demands of the task to guarantee ideal results. Appropriate cleaning and preparation of the base metal, in addition to selecting the right filler product, are likewise essential parts of proficient welding techniques. By sticking to these ideal techniques, welders can minimize the danger of porosity development and produce top quality, structurally audio welds.
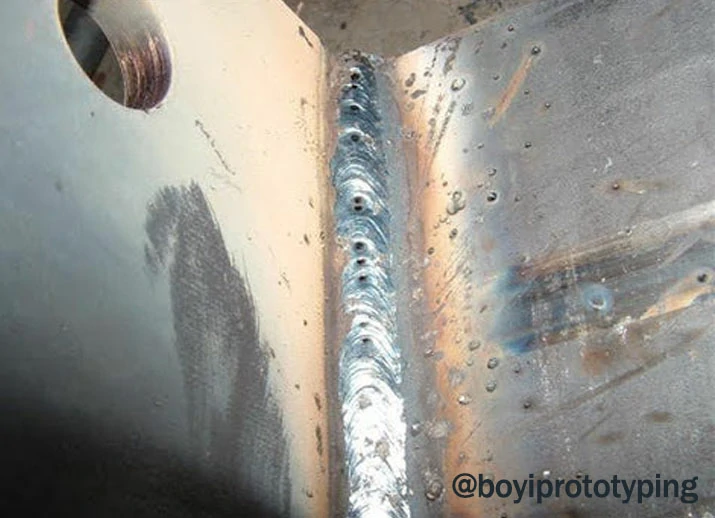
Examining and Top Quality Control Actions
Examining procedures are vital to spot and protect against porosity in welding, guaranteeing the stamina and toughness of the final item. Non-destructive testing techniques such as ultrasonic testing, radiographic testing, and visual inspection are frequently employed to recognize possible problems like porosity.
Performing pre-weld and post-weld assessments is also essential in maintaining quality assurance requirements. Pre-weld evaluations involve confirming the materials, devices settings, and cleanliness of the workspace to stop contamination. Post-weld evaluations, on the various other hand, evaluate the final weld for any issues, including porosity, and verify that it fulfills specified criteria. Executing a detailed quality assurance strategy that consists of extensive screening procedures try this site and evaluations is critical to reducing porosity problems and making certain the total top quality of bonded joints.
Verdict
Finally, porosity in welding can be a typical issue that More hints impacts the quality of welds. By determining the typical root causes of porosity and executing finest practices for avoidance, such as correct welding methods and testing procedures, welders can make sure top quality and dependable welds. It is important to prioritize avoidance methods to decrease the occurrence of porosity and preserve the stability of bonded frameworks.
Comments on “What is Porosity in Welding: Key Elements and Their Impact on Weld Quality”